Shiftall代表の岩佐です。
ESP32やRaspberry piを使って1品もののちょっとした試作機を作ったことがあるという人は増えてきましたが、いわゆる『量産品』を作った事がある人はそう多くはありません。また、大手企業に勤めていて量産品に関わったことがある人であっても、電気・メカ・ソフト・部品調達・品質評価・デリバリーなど開発の全プロセスを俯瞰して見た経験のある人は稀でしょう。
そこで本年を締めくくるShiftallブログネタとして、何十品目という家電・IoT製品のスケジュールチャートを引いてきた立場で、製品開発全体のガントチャートをどう引くか?をご紹介したいと思います。IoTの肝となるスマートフォンアプリ&サーバサイドのガントチャートについては世に山ほど解説記事があるのでここでは省略します。
まず、全体工程のパート分けを行います。
- 電気
- 機構
- 組み込みSW
- App/Server(今回は省略)
- 調達
- 品質/許認可
- 製造
ぐらいにわけておけば大丈夫ですが、調達を必ず入れるのがポイント。後述しますが、調達をミスって全体スケジュールがぐだぐだになるケースが本当に多いのです。
数回の試作フェーズを経て量産品の生産へ
ハードウェアは数回の試作を行ったあと、量産へと至ります。この試作フェーズの名称は各社それぞれ。ここではShiftall流ということで以下の4フェーズを定義しましょう。
EVT1→EVT2→DVT→PVT→MP(量産)
各名称の定義についてはこれまた山と流派があるのでWebで検索してみてください。MP(Mass Product)が量産品つまりお客様の手元に届く品で、それ以外は全て『試作機』。各試作機は当然目的があって作ります。この目的を理解出来ていないと、ゴールであるMPにいつまでたってもたどり着けないので、まずは目的を書いてみます。
EVT1(Engineering Validation Test)は、以下の目的を達成するための試作である、という点を意識しましょう。
- 目的1:さてはてこの製品、作ってみてイイ感じの使い心地なんだっけ? を検証する
- 目的2:大量に作ることを考えたとき、現実的な価格で作れるんだっけ? を検証する
- 目的3:量産を考慮した部品を使い、現実的な性能に収まりそうか? を検証する
- 目的4:どういうデザインだったら使いやすいか、かっこいいかを検証する
EVT2は一番目的がふわっとしがち。ただ、EVT2を疎かにしていると、DVTをうまく作ることができず、時間と金を大きくロストするので注意したいところ。EVT2は金型投資を行う前の最後の試作になる、ということを強く意識して設計を行う必要があリます。
目的は以下のとおり。
- 目的1:EVT1で見えた課題点に対策し、実証する
- 目的2:主要部品をFixさせる
DVT(Design Validation Test)は、金型を使った成形部品を用いた最初の試作機を指します。間違っても金型品ではない、削り出しや3Dプリント品を使った試作機をDVTと定義してはいけません。どんなに完成度が高くなっていたとしても、です。DVT前にまだまだ試作を重ねねばならないときは、EVT3, EVT4とナンバリングしていきましょう。
金型は少なくとも数百万円、多いと数千万円もの投資になるだけではなく、金型製造に1-2ヶ月という時間を要します。その期間、開発メンバーの人件費もかかり続けることも考えると、DVTをつくるぞ、という判断はとても重たいものとなるべきです。
目的は以下のとおり。
- 目的1:品質試験を実施する
- 目的2:許認可のプレ試験を実施する
- 目的3:量産品で使う部品リストをFixする
- 目的4:量産工場・量産部品のクオリティを確認する
- 目的5:量産方法(手順)を確定させる
PVT(Product Validation Test)は量産の直前に最終確認として製造ラインに流す、『最後の最後の確認のための試作』です。一般の人からは量産品との差を見て取ることは難しいぐらいなので、発売イベントの時にタッチアンドトライ品に使われたり、メディア各社への貸し出し品に使われたり、ショウルームの展示品に使われたりします。良く、メディアで『発売前の試作品のため画質(音質)などが変更となる場合があります』と書かれているのがPVTです。
目的は以下のとおり。
- 目的1:許認可の取得
- 目的2:量産実施Go/Stopの判断
改変・営利利用可能なShiftall流ガントチャートを公開
これらのフェーズ&目的を理解したうえで、スケジュール・ガントチャートを引いていきましょう。繰り返しになりますが、ここまでの内容が一番重要で、この後のチャート引きは手段にすぎません。
ガントチャートを引くツールは何でも構いません。ただ、必ずクリティカルパスを引けるツールを使うべきです。相互に干渉しあう要素が多いので、クリティカルパスをしっかりと引いておきたいのです。特定パートに遅れが生じたときに、影響するパートを動かし忘れてあれっ、となることを防ぐためです。
私が業務でチャートを引く時は、Project LibreやGantt projectなど、クリティカルパスを設定できるツールを使う。今回はBravioを試しに使ってみたのですが….クリティカルパスが設定できないんでハードウェアのガント引きにはお勧めできない感じです。
とはいえLibreで作り直すのも手間なので、このまま公開しちゃいましょう。自由に改変・営利利用いただけます。
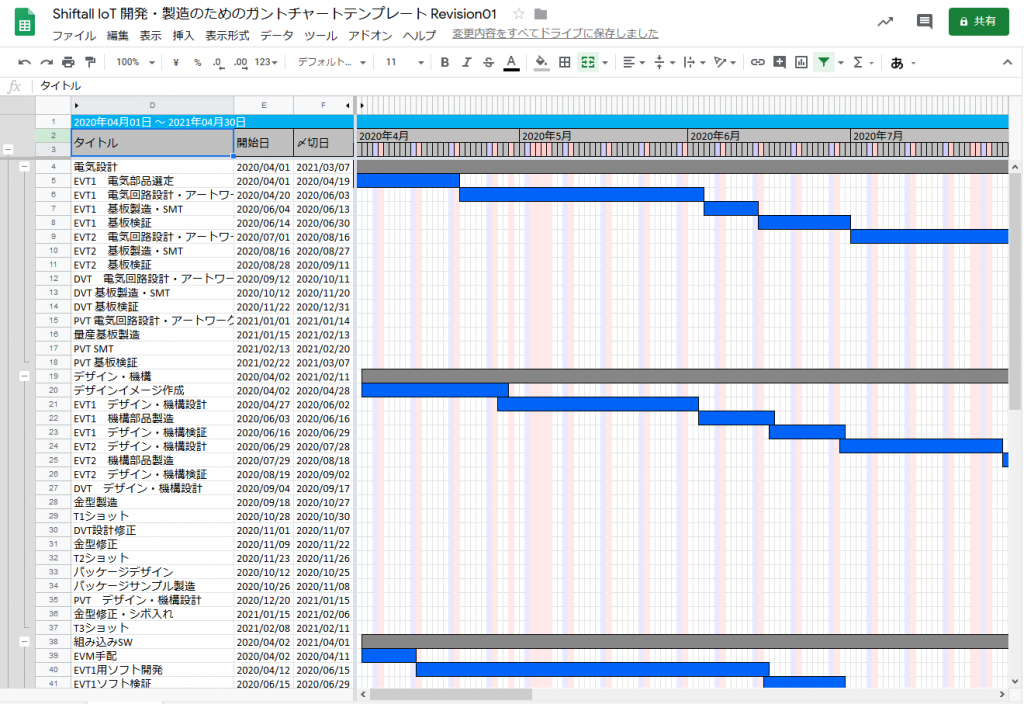
Shiftall IoT 開発・製造のためのガントチャートテンプレート Revision01 – Google スプレッドシート
https://docs.google.com/spreadsheets/d/1LiWoEqkl0JzbKlwe5yRr9XzwOHIIj5yfhbfxkXVsVxk/edit?usp=sharing
このガントチャートを引くに当たっての前提条件は以下のとおりです。
- 2020/4/1から開発を開始し、約1年で製品を量産する
- 1辺が35cm未満の小型ガジェットを想定(金型関連の時間に影響)
- 初回製造個数は1千台前後を想定
- 土日があることは考慮するが、どこにあるか、は考慮していない(なので、土日にスタートしている線もある)。週休2日であることは想定して線を引いているので、本チャートのスケジュール感から1.3倍しなければいけない、ということはない
- 休日、特にGWやお盆・年末年始休暇は考慮していない(その分+αしてください)
- 海外の工場を使う場合は現地の長期休暇を考慮すべきだが、そこも考慮していない
フェーズごとのガントチャート作成方法を解説
では順を追ってガントチャートの引き方、引く時のポイントを見ていきましょう。まずはEVT1、EVT2からスタートします。
EVT1
電気設計の視点でポイントとなるのは、最初の部品選定期間が大変短いこと。ここで全てが決まるわりには短くなっています。なので、商品企画書をみたらぱっと『このプロセッサにこのセンサを組み合わせてこんな感じの電気的制御でいけるのでは』と頭の中で組み立てられるスキルセットが必要があります。
大事なのは、ここで決めたざっくり部品選定は90%変えない! ぐらいの気持ちで選定すること。えー、本気でいっているの? と言われるかもしれませんが、1年ぐらいという短期間でモノを出そうと思うと、こうなってしまうのです。電気的にはここで肝となる部品がすべて決まってしまうので、気合をいれて最初の2~3週をこなすのだよ、ということをきちんとチームメンバーと共有することが大切です。
EVT1,EVT2の基板はいわゆるちょっぱや基板屋(JetPCB, JLPCB等)を使う前提としています。基板のLT(Lead time、調達製造にかかる期間を指す)+部品実装(SMT)を入れて10日ぐらい。
チャートの下のほうを見てもらうと、調達カテゴリのなかで2週間ほどEVT1、2用の部品調達時間を取っている点にも注目してください。基板発注してから部品手配していたら遅かったりするので、最低でも2週間前ぐらいからは部品の手配に走りたいところ。ここは電気チームと調達チームの連携が肝となります。
といってもEVT用の部品はDigikey,Mouser,AVNET等で揃えてしまえばいいのでそこまで焦ることはないのですが、一部特殊な部品でDigikey等では買えないものがあってEVT1の部品実装が始められずにスケジュール遅延する、ということがないようにしたい為です。
メカ・デザインの視点からEVT1, EVT2を見ると、デザインイメージ作成に1ヶ月弱しか取れていない点に注目したいです。ここで考えたデザインイメージを大きく変えることは難しいので、本当に重要な1ヶ月となるわけです。
電気設計メンバーと密なディスカッションをしつつ、熱設計、基板サイズ、ESD(静電気)対策のことなども考えつつ、デザインを起こしていく。デザイナーのスキルが試される1ヶ月と言えるでしょう。もっと時間をかけてデザインしたいのはやまやまなのですが、後のスケジュールを考えるとこれがぎりぎり限界というわけです。
EVT1,2の機構部品製造は2週間程度と短くなっています。これは、金型を作らず削り品を用いるため。3Dプリントだったらすぐじゃないかという意見もあるかもしれませんが、悪いことは言わないので削り品を使ってください。3Dプリントは結構お高いうえに強度的には削り品に及ばないためです。表面処理のしやすさなども考えると、EVT1の時点から削り品を使うようにしたいです。
中国国内のプロトタイピング屋(深センなどに多い)を使うと、日本国内で3Dプリントを依頼するぐらいか、下手するとそれより安い値段で削り品を作ってくれます。Alibaba.comでPrototype cnc plastic あたりのキーワードで検索すると様々な削り業者が出てくるので、幾つか相見積もりをとってみると良いでしょう。
なお、日本国内のモック屋さんのような仕上げ、精度は求むべくもないので注意してください。国内のモック屋さんは試作検討のためというよりは、展示会や偉い人が出てくる大企業の会議などで『美しい』ものを見せるという用途に特化しているきらいがあります。中国の切削業者は安かろう悪かろうであることは間違いないのですが、少なくとも我々が使っていてEVT1,EVT2の構造検討においては十二分に機能するレベルです。
Shiftallでも1月から始まるCES 2020の会場で幾つかEVT2サンプルを展示するので、ラスベガスに来られる方は『ほうほうこれが例の安い削り屋の仕上がりかぁ』と、実物を見ていただければより理解が進むのではないでしょうか。
EVT2
EVT2はシンプルな書き方をしていますが、機構屋としても電気屋としても考えることが多いフェーズです。EVT1からEVT2はある種ポーカーの手のようなもので、一体として考えるとわかりやすいでしょう。EVT1でチャレンジをして、無理だとわかったらEVT2で妥協する、といったアプローチが比較的おすすめです。
例えば、外付けアンテナではなくチップアンテナで行けないか試してみよう、本当は通気孔が必要かもしれないけどかっこ悪いしナシでいけないか試してみよう、などとチャレンジするのがEVT1。EVT1の検証後に、やっぱり電波飛びがわるいんで外付けアンテナにしよう、やっぱり熱対策難しそうなんでEVT2では通気孔を付けよう、といった具合に妥協点に落とし込むわけです。
どことどこをチャレンジしていて、何をもってダメと判断するか、どういう妥協案を考えているか、がリストになっていると良いでしょう。最終判断するマネージャーがこのリストをちゃんと把握できているかどうかはスケジュールに直結します。
続いてソフト屋の視点からのEVT1です。EVT1開発中の組込みソフトウェア開発は他のパートとくらべてちょっと特殊かもしれません。というのも、EVT1基板が完成して手元に来ない限り、EVT1用のソフトウェアを開発することができないからです。
ではどうするのかというと、EVM(EValuation module)やEVK(EValuation Kit)と呼ばれるチップセットベンダーが提供している開発用基板が入手できることが多いので、これらを入手してEVT1基板が来たときに焼き込んで動くであろうソフトを作り始めておくのです。
EVM/EVKとはこのようなものです(こちらはNXPのi.MX8用EVK)
i.MX 8M Evaluation Kit | NXP
https://www.nxp.com/design/development-boards/i.mx-evaluation-and-development-boards/evaluation-kit-for-the-i.mx-8m-applications-processor:MCIMX8M-EVK
正直組み込みソフトは独立してもっと細かくガントチャートを引くべきなのですが、ソフト開発のガントチャートは世に溢れていることもあり単純化しました。
さて、EVTの締めは品質・許認可のパートです。商品名検討や意匠・商標調査の時間をEVT2開発中に入れてあります。EVT2あたりから展示会などに出すケースもあるし、金型着手してしまうと形状はもう変えられません。金型に製品名を彫り込むケースもあるので(エンボス)、ここで決めて&調査しておきたいものです。
DVT
EVT1,EVT2についてはこれぐらいにして、DVTを見ていきましょう。DVTは超重要ということは前述したとおりです。
電気の視点でDVTを見ると、基板製造を4週、実装もいれると5週と長く置いています。これはDVTからは量産で使う基板製造工場を使うべきで、量産用PCB製造工場の標準的なLTは4週程度かかるためです。
DVTの重要な目的の一つは、先に書いたとおり品質関係の試験となります。よって、本番で使う基板で品質試験を実施しないと意味がないわけです。
といってもこれは理想論で、実際にはスケジュールが厳しくなってしまうと、試作向け基板屋を使ってDVT1を作り、追ってDVT2として本番基板を使った試作機を用意して試験はそちらで通す…という裏技もよく使われますが、本ガントチャートでは正統派のやり方にて線を引いておきました。
機構の視点からのDVTは、金型を作るというこの1点に集約されます。とっても重たい判断なので、金型発注は慎重に行ないましょう。なお、中国国内の金型屋においては、50%が前金、50%は完成後支払いというのが一般的です。
金型完成後に最初の射出成形を行うことをT1ショットと呼びます(1st test shotの略)。射出だからShotというわけです。
T1に向けては金型の表面仕上(シボ、磨き)などは行ってはいけません。時間を節約するためでもありますし、どうせこのあとの試験結果で何らかの金型修正が入るので、シボ・磨きぶんのコストも高い確率で無駄になってしまいます。この段階では外観を見ることではなく、試験をして数値を知ることができれば十分です。
このチャートでは、T1ショットでちょっとした問題がみつかって、すぐに金型修正をしてT2ショットを打つ、という想定としてあります。T1品を作ってみたら、基板を入れるまでもなく『あー、ここでミスった!』という点が出てしまうことが多いので、そのように引いてみました。
電気屋側ではDVT基板製造に時間がかかっているので、そこを横目で見ながら『DVT基板が仕上がるまでにT1を作ればいいんだよね』とのんびりやってしまうと、T1ショットで問題が見つかったときにDVT試験に移行することができず、金型修正~T2ショットまでの時間分、電気屋を待たせてしまってトータルスケジュールが遅延してしまいます。必ずT1ショットを早めに打って、型修正の時間を取れるようにしましょう。
機構パートのなかにパッケージデザイン、パッケージサンプル製造とある点も注目したいところです。DVT品を使った品質試験のなかに、パッケージに入れた状態で落下させる試験(梱包落下試験)や、パッケージに入れた状態で振動させる試験(梱包振動試験)があるため、ここでパッケージサンプルを作っておかないといけないわけです。
サンプルなので、ダンボールを買ってきて自分で切って作るといったレベルで構いません。もちろん、パッケージ屋に依頼して作ってもらうことができれば理想です。
パッケージはこだわりたい、という会社が多いようですが、そんな会社であればもう少し前からこの工程に入ってもいいかもしれません。何れにせよ、最低でもこれぐらいの時期にパッケージ構造はFixしておかないといけない、と覚えておきましょう。当然ですがパッケージ印刷の内容などはもっとずっと後で構いません。ここで重要なのは素材と構造のみです。
調達・品質試験
さて、このあたりではじめて調達パートが出てきます。10月1日からLT(Lead Time、調達機関)の長い『長LT部品手配』という線が引かれているところに注目してください。だいたいどんな家電製品であっても、1つや2つはLTが20週というような部品を含んでいます。ハードウェア開発・製造にはじめて関わるという人がよくびっくりするポイントかもしれません。
EVT2の設計完了時点で(完成時点ではない!)、必ず全部品のLTを確認するようにしたいです。この例だと、8月末にその時間を取ってあります(調達パート内)。
DVT開発が終わったら、いよいよ製造にむけてのカウントダウンとなる品質試験がはじまります。品質・許認可のパート内にDVT品質試験として1ヶ月置いてあるのがそれです。ここで様々な品質試験を行います。落下試験、高温/低音動作試験といった誰もが想像するものから、安全系の試験(短絡試験、非防水機器への水かけ試験など)など項目は多岐にわたります。
同時に許認可系プレ試験という線も引いてありますが、これは電波モノであれば工事設計認証(いわゆる技適)系の試験、コンセントにつなぐ機器であれば電気用品安全法といった法律系、許認可系の試験と同等レベルの試験を実施して、実力値を見ておくことをいいます。こればっかりは、量産直前にやる最終試験に落ちてしまったら、発売できなくなってしまいます。必ず事前試験をやって、本番試験に向けて対策が必要なのかそうでないのかを見極める必要があるわけです。
例えば雑音端子電圧試験をやってみて、ちょっとしたフェライトコア追加で何とかなるレベルなのか、根本的に回路設計から変えなければいけないのかを見る、といった風に。ここで試験しておけば、PVT基板設計時に回路へと対策を入れることも可能です。
PVT
さて、ついにPVT準備に突入します。
DVTが完成して一通り試験が終わり、結果がそれなりに良いものであれば、量産が目の前に見えてきたと言えるでしょう。ここからは全パートで細かいToDoが乱立するので、このチャートを参考にやり残しがないようにしていってください。1個でも抜けていると、その分の時間スケジュールが後ろに倒れてしまうという、怖い時期でもあります。
電気パートでは、先のDVT評価結果を反映した量産基板のデータを作ります。PVT基板=量産基板なので、ミスできない電気屋最後の大仕事。基板に入れるシルクパターンのレビューも忘れないようにしましょう。基板シルクでPVTとか書いちゃった日には恥ずかしいことになるので注意。
製造パートのところに書いている『量産治具作成』は電気屋とソフト屋の合作です。量産工場のライン上で使うFirmware書き込み治具や、基板単位でのFunctionTestを行うためのピン治具ならびにそのソフトなど、製品によって治具はさまざま。これをきちんとスケジュールに入れておかないと、工場から『そんなんじゃ作れないよ!』と言われてしまい、治具が完成するまで量産スケジュールが押してしまいます。必ず工場と密に話し合いながら作っていきましょう。
機構パートはいよいよ金型をFixさせるタイミングです。T1,T2では入れていなかったシボを入れ、表面磨きも行って量産用ショットとなるT3またはT4を目指します。シンクやウェルドを軽減するといった意匠に影響する成形条件の微調整もここで行うので、このタイミングはデザイン・機構の担当者は金型工場・成形工場に張り付きとなるケースが多くなります。事前にメンバーには了承をもらっておきましょう。
ソフトウェアパートは先に述べた治具用のソフトを忘れずに作りましょう。ラインのうえで製品に書き込むファームウェアにも検査モードを実装することが必要なので注意。メモリ容量カツカツの商品などでは、工場検査用ファームウェアを書いてライン上でFunctionTestを実施し、問題がなければ最後に出荷用ファームウェアに書き換えて出荷という手順を踏むこともあります。
が、これはあくまで例外的なやりかたです。基本は、同一ファームウェアにしておいて、特別な操作によって工場検査モードに入れるようにします。
工場検査モードで検査に落ちた製品は、出荷モードに切り替えることが出来ないようなソフトウェアとしておくことが大切です。例えばLAN接続して治具PCから特定のパケットを受信できないようならば、検査モード上で『Ethernet端子NG』と出て、出荷モードに切り替えられないよう作ります。工場でのミス、見落としはどうしても起きてしまうので、こういった不具合品がうっかりで出荷されないよう、工場検査モードの設計でカバーするというわけです。
検査モードには必ずバーンイン試験モードも用意しましょう。完成品を数時間、全力で動かして壊れないか見るモードのことをいいます。製品に備わっている可能な限り全ての電子デバイス・物理デバイスを高負荷で動かして、製品の実力値を確かめます。通常、製品版Firmwareには何時間も全I/Oを動かすような動作モードは無いため、バーンインモードとして特別に用意する必要があるのです。忘れずに!
調達パートも全期間中もっとも忙しくなるタイミングです。長LT品を除くと、一般的な量産部材はだいたい2ヶ月程度で手配できることがほとんど。部品集結日として設定した3月1日をめがけて、大量の部材の調達をかけていきます。
短LT部品手配とシンプルに書いてはいますが、Excelとにらめっこしつつ各サプライヤーに連絡して部品手配をかけまくりましょう。もちろん、部品調達を工場に任せてしまうようなケースでは、工場に対して部品手配かけてくれよな、部品リストはこれだぜ、というやり取りをすることになります。
製造パートには見慣れない単語が並んでいると感じる人も多いかもしれません。組み立てにあたっての注意事項をまとめ、こういう手順で組み立ててください、という手順書(組み立て指示書)は忘れがちなポイント。
ねじを締める部分は全てトルク管理です。何ニュートンで締めるのか? も書くのを忘れないようにしたいです。
両面テープを使うならどこのどんな仕様のテープなのか、グルーを塗るなら何ml塗布するのかなどあらゆる要素を定量的に書く必要があります。
なれてしまえばかんたんなのですが、最初に作るときはちょっと難しいので、工場に言って参考になる組み立て指示書を見せてもらうのが良いかもしれません。自社製品を持っている工場であれば快く見せてくれることでしょう。
再試験・リワーク
PVTが完成したら、DVTのテストで落ちてしまった項目の再試験をします。もちろん、DVTで実施した試験をもう一度全てやり直すのが理想ですが、時間的に厳しいことが多いので落ちたところに項目を絞って実施すればよいでしょう。もちろん、DVT→PVTで変更を入れたことによって影響しそうな項目は、たとえDVT試験で合格していても再試験が必要ですが。
許認可系の本試験は、出荷までに通っていればいいことがほとんどなので、MPの時間に食い込む形でスケジュールを引いてあります。もちろん、万が一試験に落ちてしまったら製造全部やり直しになってしまうのでリスクはあるのですが。
一度良品として工場の製造ラインをロールアウトした量産品を再度分解しなおして何らかの不具合対策を実施することをリワークと言い、家電業界三大聞きたくない単語の1つにランクインするなど(当社調べ)忌まわしき言葉です。リワークだけは避けたいのですが、スタートアップに限らず大きな企業でもちょいちょい実施していたりする作業です。
もちろん、本ガントチャートにはリワークなぞ定義していません。ただ、回路や機構の問題は起こらない前提としていますが、ソフト屋のパートの最後に『第1回Firmware update用のソフト開発』という線を引いてあります。最悪、出荷したあとでもお客様のところに最初に届いた時点でFirmware updateを掛けて問題を解消できることがある為です。これが最後の砦となります。
量産
初回ロットの量産は数百~1,000台程度を想定して線を引いたので、基板実装(SMT)で1週間、組み立て(Assy)で2週間程度と短くしています。これぐらいの期間を想定しておけばぎりぎり足りるはずですが、のんびりやっているとSMT+Assyで3週間というのはすぐに過ぎ去ってしまいます。工場に張り付いてお尻を叩く、自分たちは急いでいるんだぞというのを工場にきちんと伝えるという前提での期間だと理解してください。
量産前はサプライヤーからの部品入庫チェック基準(IQAレベル)を決めてほしいとか、量産ラインでの傷や塗装ムラなどをどのレベルならOK/NGか(リミテッドサンプル)を決めてほしいとかの、細かい製造まわりタスクがばばーっと走ります。一例を書きましたが、他にも沢山の細かい工場調整タスクが走るので、1~2週間は工場に張り付く必要があると思っておくとよいでしょう。
輸送・輸入通関で1週間と置いているのは航空便を想定しています。船便だともう少しかかってしまうので注意しましょう。初回ロットはエアで飛ばし、次回ロットから船便というのがギリギリカツカツなプロジェクトではよく使う手です。
さいごに
長文になってしまいましたが、あんまり深く考えずにだいたいこんなもんだよね、という線表を引いてみたらスタートからちょうど1年でデリバリーという時間軸になりました。私が色々なところで『まぁ1年ぐらいあればハードウェア作れますよ』と言っているのは、ほぼこの線表が示すところとなります。もちろん、作る製品や関わるチームメンバーによってスケジュールチャートは変化すべきであり、あくまで参考にしかなりませんが、これからはじめてハードウェアに関わるぞという人達にとっては、重要なたたき台になるはずと思って書いてみました。
2020年にハードウェア・スタートアップをはじめてみたいという方、これから自社の事業で家電・IoTに絡んでみたいのだという方の参考になれば幸いです。それでは皆さん、良いお年を!